Wire Selection for Harnesses and Cables
- DECA Manufacturing
- Mar 18, 2021
- 2 min read
Updated: May 17, 2021
Conductors
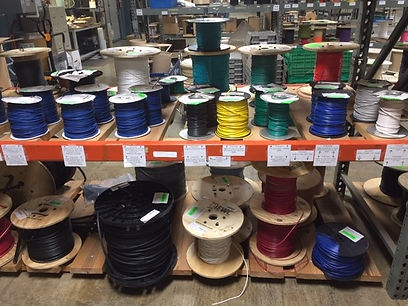
When folks think of wire they tend to think of copper, but there are many kinds of wire used in cables and harnesses including:
copper plated with other metals such as nickel, tin,and silver
alloys such as beryllium-copper, cadmium bronze, alumel
fiber optic cable made with either plastic or glass
No matter what the material of the conductor/wire, it is available in a variety of gauges or sizes. Selecting the proper gauge depends on the amount of power and/or data being transmitted and the length of the cable. Since different types of wire have different physical and transmittance properties, selecting the proper gauge is critical. Wire with larger diameters, lower gauges, carry heavier loads and are better suited for larger appliances and industrial applications. Wires with smaller diameters, higher gauges, are best suited for small appliances, delicate medical instruments, etc.
Insulation and Jacketing
Since bare wires are not used in components, virtually all wires have a layer of insulation which is typically either thermoplastic or thermoset plastic. The latter, which is more expensive, is typically used when the wire harness or cable assembly is going to be exposed to high temperatures and must not melt and must remain flexible. The list below shows some common types of plastic used for wire insulation.
Thermoplastic: PVC (Polyvinyl Chloride), PE (Polyethylene), ECTFE, PVDF, Nylon
Thermoset: XLPE, CPE, EPR, Neoprene
In addition to insulation, wires may require an additional protective jacket which could be made of a nylon, cotton, glass, Kevlar or metal sheathing. The type of wire insulation and additional jacketing depends on the application and operating conditions the finished wire product will be exposed to. For example, if the cable is for aerospace or industrial use, the cable will require high level of ruggedization to ensure
Toughness, tear and abrasion resistance
Flexibility during cable installation, at low temperature
Stability over a range of temperatures
Resistance to heat aging
Resistance to cable deformation
Low moisture absorption
Oil resistance
Resistance to abnormal concentrations of chemicals
Weather or ultraviolet resistance
Wire Configurations
In addition to the actual type of wire and its jacket, wire comes in dozens of configurations. Listed below are just a few:
single strand, aka single conductor
multi-strand, including duplex, triplex, or quadruplex
multicore
ribbon format
Processability
Lastly, how easy is it to process the wire? This simply means how easy/difficult will it be to cut, strip, and add the desired connectors to the wire. While processability may not affect the final product’s function, it may affect the price to manufacture the wire harness or cable assembly. For example….if the wire’s end usage is in a medical product will it be easy to strip the insulation with a laser wire stripper? If the jacketing is woven, does it fray too easily? Is the insulation’s melt point high enough to permit needed welding, potting or other manufacturing operations?
These are just some of the factors that product designers should consider in regards to what we call your product’s nervous system-- the design of the wire harness or cable assembly. It is critical that material decisions be not solely on the basis of cost, but on the application and operating environment. Finally, the materials selected should be compatible with the manufacturing process as well.
Partner with Us for Your Next Project.
Would you like a partner for your next project to ensure your final product’s success? DECA prides itself on being responsive, smart, and flexible. Contact us today!
Comments