Smart Manufacturing with Great Cables
- DECA Manufacturing
- Dec 3, 2020
- 3 min read
Updated: May 17, 2021
Cable Assemblies, Wire Harnesses, and Box Builds Enable IoT on the Factory Floor
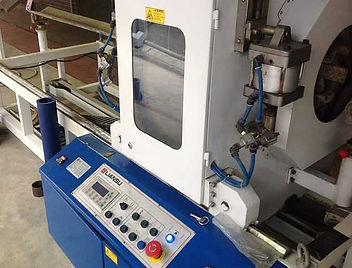
Unlike older systems, smart manufacturing equipment requires more than just a simple power cord. New systems often require wire harnesses or cable assemblies with multiple sensors and wired connections. In addition to providing power, wire systems on production equipment sends data from various sensors to a transmission or storage point. In other words, today’s high-tech manufacturing devices function like your nervous system by sending the signals that guide and track functionality. When these wired connections are combined with box builds/system integrations smart production systems are able to
transmit production data to the cloud for real-time reporting and visualization
start and stop machinery based on pre-established parameters such as work completed or safe-operating parameters
send out notifications about operating conditions, changeover, and work completed
Given the critical nature of the data and the conditions in which these cables function it is important to make sure that cable assemblies are of the same caliber as the machines they support. Industrial equipment is expensive; its purchase is an investment in the company and its future so it needs to be durable and a good value for the money. Though often overlooked the data/power cables these machines rely on should be high quality and ruggedized. Building great cables means that quality includes both the raw materials and actual assembly work.
Why Manufacturing Equipment is Evolving
Cables and wire harnesses for shop floor equipment used to be very simple; they primarily provided power. While common industrial equipment such as CNC Mills, pumps, conveyor belts, and blast furnaces; had basic monitoring, most of tracking was handled by personal observation and simple gauges. Information was noted at each individual machine, recorded, and then transmitted, often using paper-based logs. It was a time consuming process.
Why IoT Makes Sense for Production
Production equipment has evolved tremendously. Equipment can be outfitted with an array of sensors that can gather real time information about just about any facet of manufacturing imaginable including:
lubrication levels
environmental conditions
operator performance
production levels
work order status
quality results
This information is then be relayed via wireless networks to the cloud or centralized hubs where the data is used to gain actionable efficiency insights, plan maintenance, monitor overall production, identify employee training needs and more. Depending on the sophistication of the software and systems, equipment can send messages via cellular networks to alert managers of problems on the shop floor. This evolution of “smart” equipment, is commonly referred to as the Internet of Things (IoT) or sometimes more specifically the Industrial Internet of Things (IIoT) in the commercial manufacturing world. It has enabled manufacturing efficiency advances at a pace and scale that is unprecedented.
We Understand Smart Production Because We Use it
At DECA we not only manufacture the cables and box builds that support Smart Manufacturing, we use it on our shop floor. We understand how the conditions under which smart devices operate will dictate:
the design of the wiring components needed to efficiently transmit power and data
the types of wire and terminations best suited to your application
the best way to future-proof your design with the expectation of more data capture and transmission to come
options for ruggedizing cable assemblies and components for long-term reliability in any environment
Contact DECA for your next IoT Project
Do you build manufacturing or other types of smart industrial equipment? What can we build for you so your finished products work smarter, not harder? Contact us today for a quote.
Comments